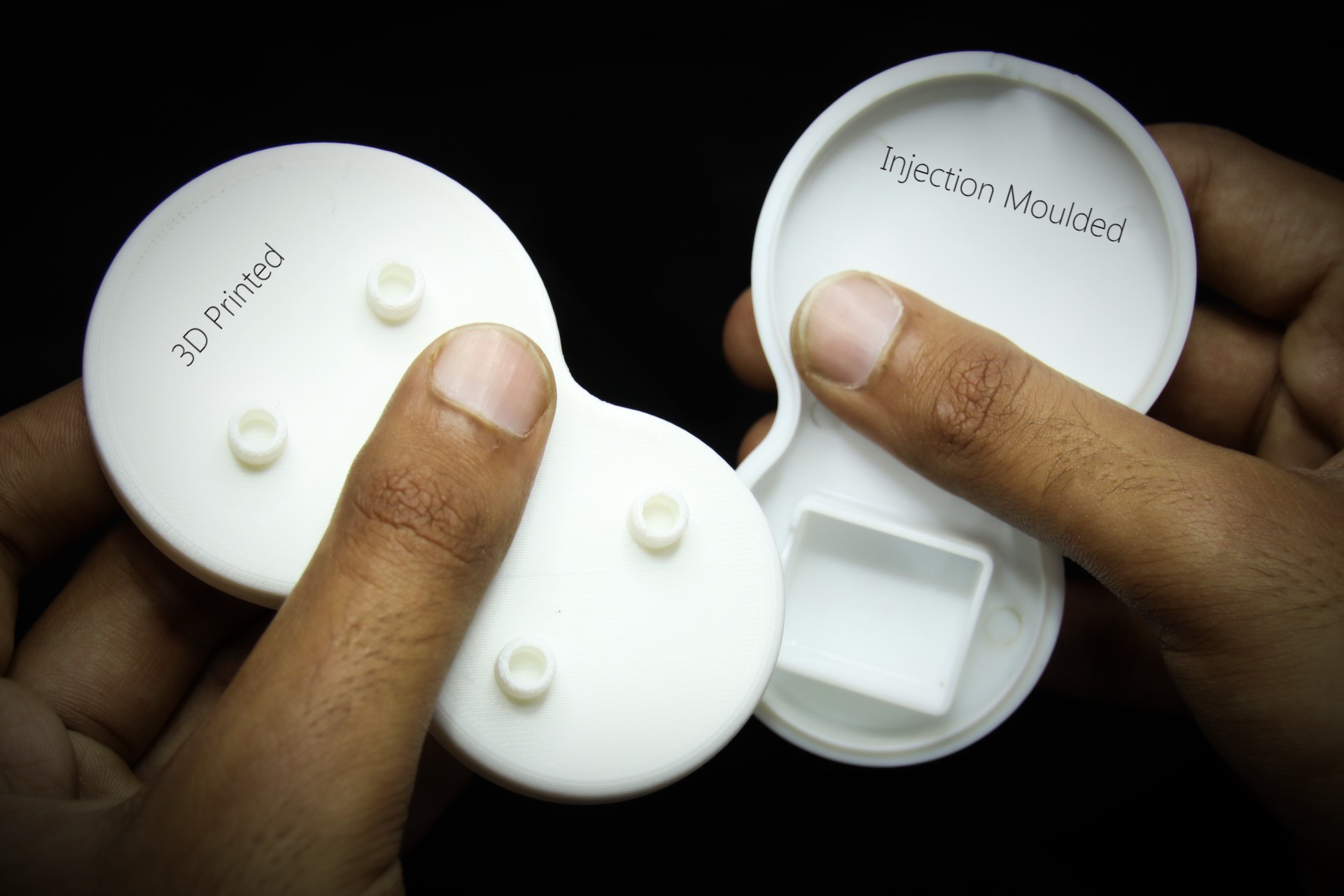
Plastic injection moulding and 3D Printing are the manufacturing methodologies that make unique and customized products. These technologies are used by manufacturers for more accessibility and are used in many practical, real-world applications.There are many benefits of using plastic injection moulding over 3D Printing. So, we will compare plastic injection moulding vs 3D Printing to help you decide the best one that suits your manufacturing needs.
Plastic injection moulding
The process of plastic injection moulding is a manufacturing technique used to produce a wide variety of parts and products. This process is typically used for high-volume production. Injection moulding is a popular manufacturing process because it is relatively fast and inexpensive.Because of its affordability, it is one of the world's most commonly used manufacturing processes. It is also a quick and efficient way to produce large quantities of plastic parts. Injection moulding can produce parts with complex shapes and parts with features that would be difficult or impossible to build using other manufacturing processes.Injection moulding is also a very versatile process. A wide variety of plastics can be injection-moulded, and we can use injection-moulded parts in a vast range of applications.
Applications of plastic injection moulding
Plastic injection moulding has been developed to mass-produce plastic products for industries and individual use. It is one of the easy ways to create complex parts of products, from toys and household items to medical devices and car parts.Plastic injection moulding has many applications in different industries. In the medical industry, for example, it is used to create prosthetic devices and implants. In the automotive industry, it is used to make car parts, such as dashboards and bumpers.
3D Printing
3D Printing, on the other hand, is a growing technology used to create three-dimensional objects. This technology is typically used for low-volume production or prototypes, and 3D Printing is expensive and slower than injection moulding but offers more design freedom.
Differences between plastic injection moulding and 3D printing
The main difference is that plastic injection moulding is a flexible manufacturing process, while 3D Printing is a rigid manufacturing process.A 3D-printed part is more robust than a part made with plastic moulding. Plastic injection moulding uses hot melt extrusion to produce parts, requiring high temperatures and precise mechanisms.In addition, the parts produced with plastic injection moulding can be lightweight and easily manipulated. Because of this, manufacturers can make highly functional products much faster with larger margins using plastic injection moulding.On the other hand, 3D Printing uses cold material printing to produce parts, requiring low temperatures and heavy-duty machines. Therefore, a component made with plastic injection moulding can be much lighter and less durable than a part printed with 3D printing technology.Tooling design is one of the most time-consuming parts of injection moulding, whereas, for the same tooling design, it takes less time for 3D Printing. Plastic injection moulding uses less energy than 3D Printing. Therefore, it's ideal for rural areas that don't have access to electricity to produce spare parts.
Conclusion
Plastic injection moulding and 3D Printing are promising manufacturing processes that can produce unique products for consumers' needs. When it comes to choosing the right one for your project, it always depends on the quality, quantity, and type of product you are trying to manufacture.You can control about 75% of product costs in your design and prototyping stage. Because this stage ultimately affects all your manufacturing, assembly and even raw material costs. Despite your firm's design for manufacturing (DFM), prototyping will always be a vital decision driver at every stage.Thus, remember to design, 3D Print, validate and repeat until production, i.e. injection moulding. We hope this article helps you to choose the right manufacturing technology for your project and work.Get an instant quote by 3D Printing