Injection Moulding Services
Get custom plastic moulded proto and production parts in as fast as 7 working days.
.avif)
Our Injection Moulding Capability
Ensure superior accuracy, efficiency, and timely production for your high-quality injection-molded parts. From concept prototypes to full-scale production components, every piece is crafted with precision using advanced manufacturing processes, guaranteeing durability and performance.
Plastic Injection Moulding
For your high resolution production grade parts in low to high volume production.
.avif)
Over/Insert Moulding
Two phase Injection Moulding. Molding over the metal inserts or plastic part.
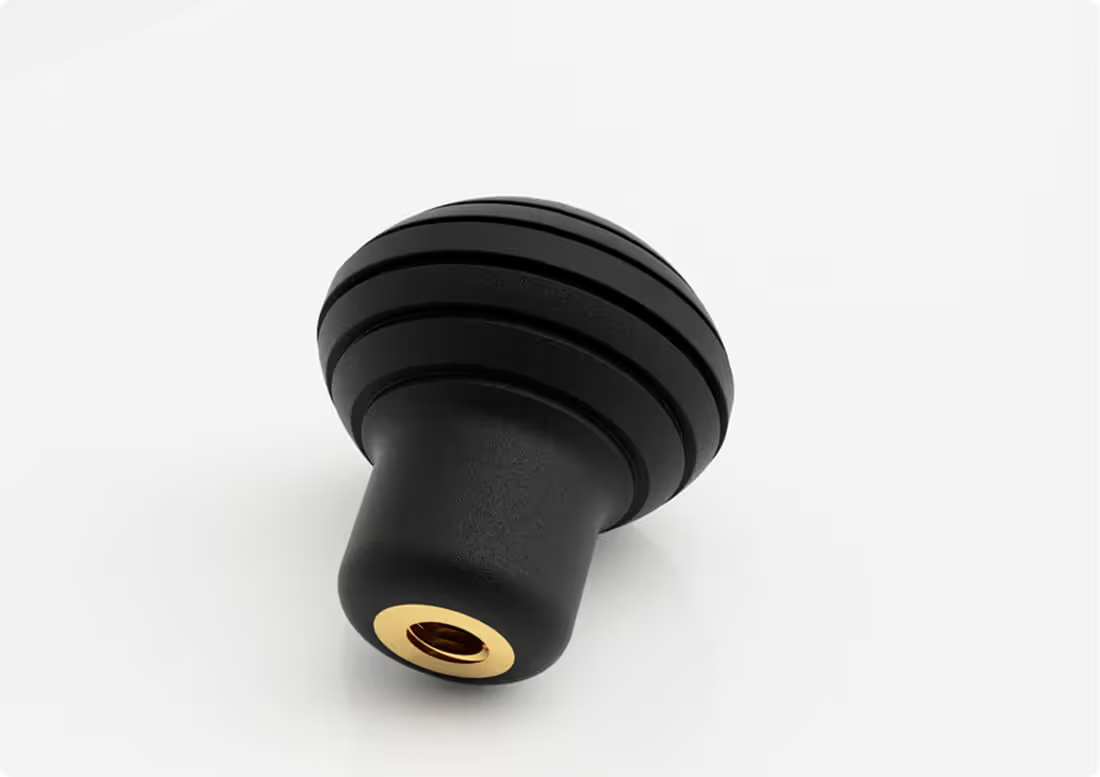
Free DFM Feedback
Get best out of Plastic injection moulding with DFM
Get free insights on part draft, parting line, gate and ejector pin points ahead
Precisely plan your crtitical to quality features with our feasibility study
Confidently mass manufacture your high quality parts with us
.jpg)
Rapid tooling to Production Tooling
We deploy Aluminium moulds for your low volume production starting from mold class 105 that span over 500 shots. Once you are ready we manufacture your moulds with German Steel Thruhard Supreme® which lasts over 1 million shots.
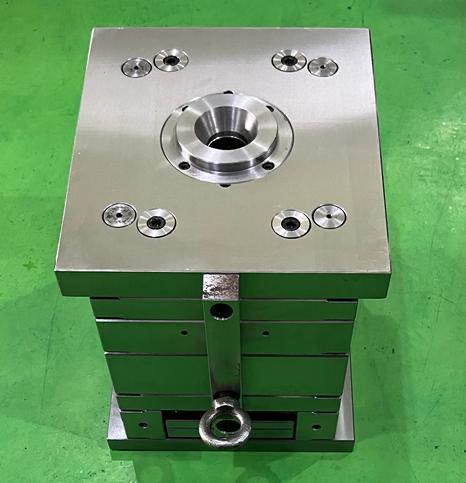
Our Secondary Services
When manufacturing with injection molding or 3D printing, additional operations may be needed to meet project requirements. We provide Secondary Services to enhance functionality and branding.
.avif)
To have permanent markings on the surface. A precise laser beam is used to achieve a quality finish.
.avif)
To have permanent markings on the surface. A precise laser beam is used to achieve a quality finish.
.avif)
To have permanent markings on the surface. A precise laser beam is used to achieve a quality finish.
.avif)
To have permanent markings on the surface. A precise laser beam is used to achieve a quality finish.
.avif)
To have permanent markings on the surface. A precise laser beam is used to achieve a quality finish.
.avif)
To have permanent markings on the surface. A precise laser beam is used to achieve a quality finish.
Injection Moulding Materials
Find out the detailed portfolio of our injection moulding materials we deal with.