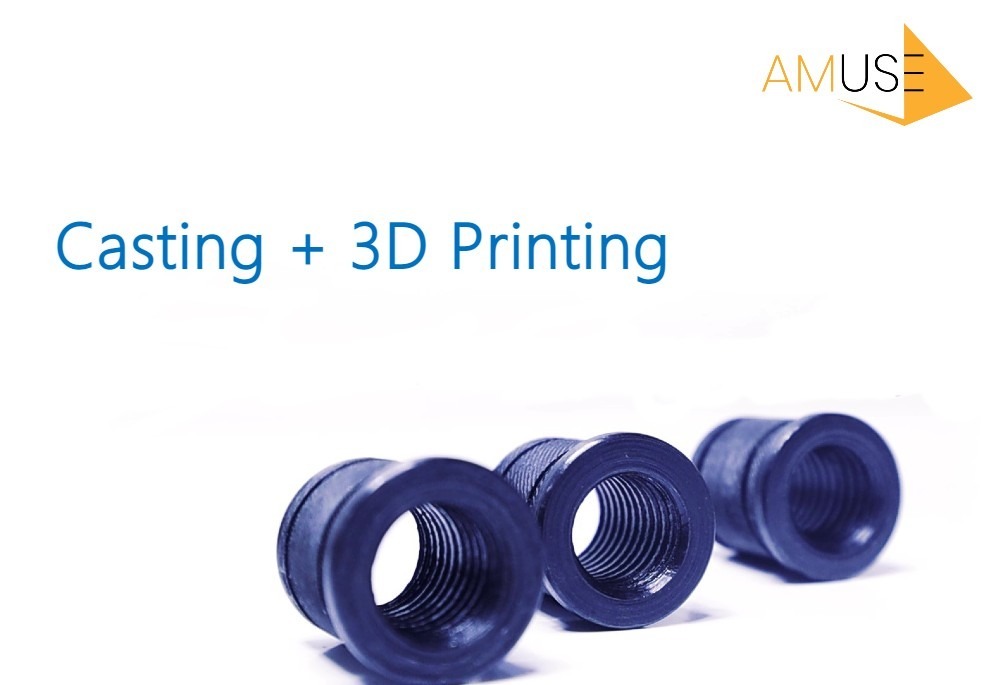
3D printing and casting are two distinct manufacturing technologies with benefits and limitations. While 3D printing offers the ability to create complex geometries and customized products, casting is best suited for mass-producing simple objects and metal parts.However, combining the two technologies makes it possible to achieve the best of both worlds and create high-quality, customized products that would be difficult or impossible to achieve with either technology alone. This article will discuss the ways to combine them and their advantages and benefits.
3D printing with casting workflows
One of the most common ways to combine them is by using 3D printing to create moulds and patterns for casting. This allows manufacturers to develop moulds and patterns quickly and easily without requiring extensive tooling and setup times. Besides, 3D Printing allows the creation of customized moulds and patterns, which can be tailored to a customer's specific needs.The aerospace and automotive industries are already taking advantage of this technology and are using 3D printing to create moulds and patterns for casting metal parts, such as engine components and landing gear. The medical industry also uses 3D printing in casting processes, particularly in producing customized prosthetic limbs and dental implants.Another way to combine both is by using 3D printing to create complex casting moulds that are difficult to achieve with traditional casting methods. This process allows manufacturers to develop optimized parts for strength, weight, and functionality without requiring extensive tooling and setup times.However, it's essential to keep in mind that some challenges and limitations come with combining them. For example, the current 3D printing technology still needs to be improved regarding materials and precision. Additionally, while 3D printing is excellent for small-scale and customized fabrication, it may still need to be capable of mass-producing products on a large scale.
Benefits and advantages of combining them
There are several benefits to combining 3D printing with casting workflows, including:Increased design freedom: It allows for the creation of complex casting moulds and customized products. This increased design freedom can lead to the creation of parts optimized for strength, weight, and functionality.Reduced lead times: Traditional casting methods can be time-consuming and require a long lead time. By using this to create moulds and patterns for casting, manufacturers can reduce lead times and produce parts more quickly.Reduced tooling and setup costs: 3D printing eliminates the need for extensive tooling and setup times, saving manufacturers significant time and money.Improved accuracy: 3D printing allows for the creation of moulds and patterns that are highly accurate, which can lead to better quality parts.On-demand production: 3D printing enables on-demand production, which means a product can be created when needed without needing a large inventory.Scalability: The combination of these technologies allows for the production of small-scale and customized parts and the mass production of metal parts.Material options: 3D printing allows for the use of a wide range of materials, including plastics, metals, ceramics, and even food, to create moulds and patterns for casting.Improved safety: It eliminates the need for manual labour and can reduce the risks of accidents and injuries in the casting process.Environmentally friendly: 3D printing reduces material waste and energy consumption.
Conclusion
In conclusion, combining 3D printing and casting workflows offers a range of benefits, including increased design freedom, reduced lead times, and the ability to create customized products. Many Industries, such as aerospace and automotive, are taking advantage of this technology and are seeing good results. However, evaluating your project's needs and selecting the most appropriate technology is essential. It is evident that this will play a prominent role in the future of manufacturing.