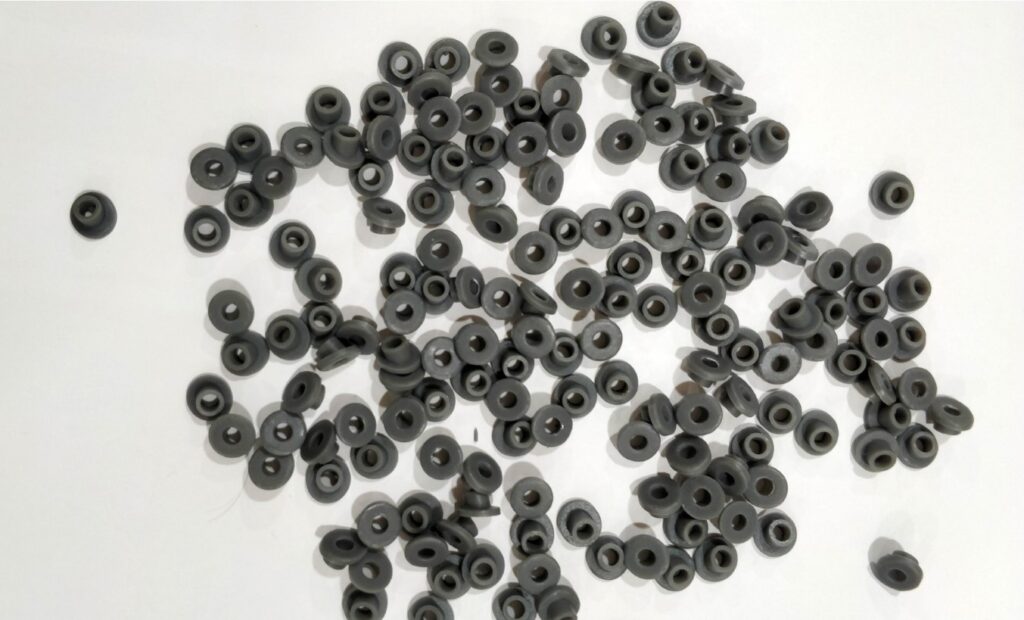
The core feature of an application, incredibly dependent on the materials we choose. Thus, it is essential to plan before manufacturing the part. To identify the exact material to suit your requirement. And enable absolute performance - we have made this material insight to ease your decision making process.This material collection includes a wide spectrum of materials with 3D Printing. Here we highlight the parent polymer and the corresponding 3D Printing technology by which we could process.In this article, we wanted to cover a range of thermoplastic. However we will also discuss some application based resins which are thermosetting in nature.Thermoplastic pyramid below delineates their performance. And mechanical strength and their cost increases towards the top of the pyramid. In practice, all the materials in this pyramid can be processed in Fused Deposition Modelling 3D printing technology.
ABS:
ABS (Acrylonitrile Butadiene Styrene) is commonly plastic. Valued for its strength and safety, ABS is a popular option for home-based 3D printers. The material consists of pasta-like filaments that give ABS its firmness and flexibility.ABS is available in various colors that make the material suitable for products like stickers and toys. Increasingly popular among craftspeople, ABS is also used to make jewelry and vases. ABS is water and chemical resistant and does produce an unpleasant smell when heated.Because of the chemicals released in the vapor, it needs good ventilation. ABS is broken down by UV radiation, losing its color and becoming brittle, so it is not suited for extended outdoor use.
PLA:
Another crowd favorite in 3D printing materials is PLA, a cornstarch derivative (but sugar cane and tapioca varieties can also be found), which makes it biodegradable. It‘s an easy material to 3D print with and emits a pleasantly sweet fragrance when heated. For this reason, many people prefer it over ABS.Moreover, it is a suitable 3D printing material for single-use food contact and it contracts less than ABS when cooling. However, PLA is less durable than ABS and susceptible to heat.PLA lasts a long time under normal conditions. It is biodegradable and breaks down when buried in the ground. Prints can shatter under stress. Some manufacturers make what they call ‘tough PLA’ by adding chemicals, creating PLA that is less brittle and more heat tolerant.
NYLON:
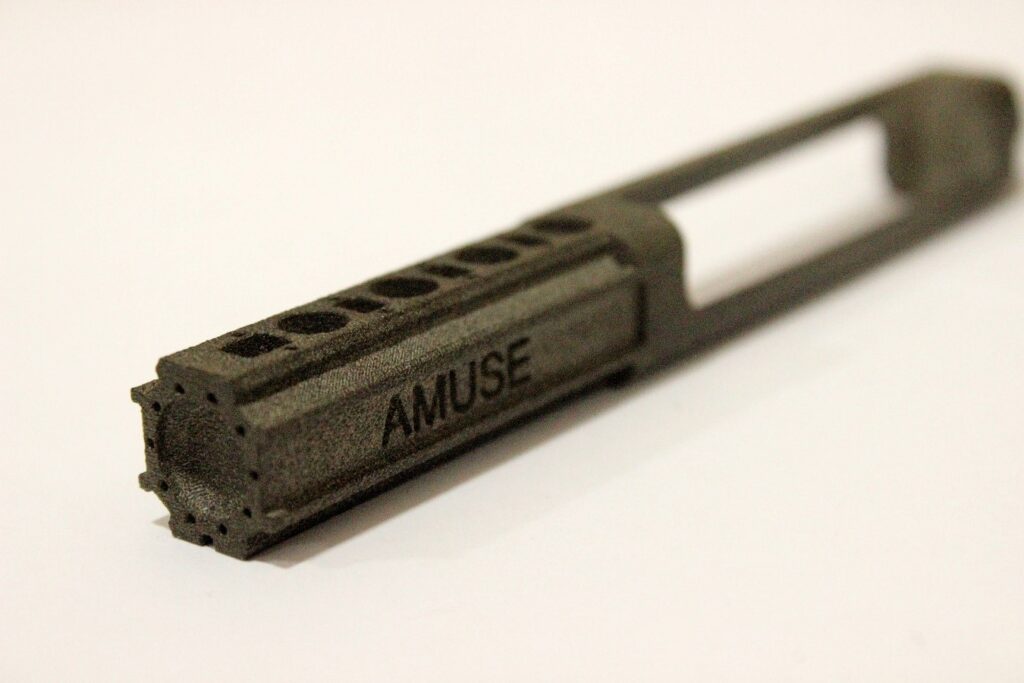
Nylon (known as polyamide) is a synthetic thermoplastic linear polyamide and is the most common plastic material. It is a well-known 3D printing filament because of its flexibility, durability, low friction and corrosion resistance.Nylon is also a popular material used in manufacturing of clothes and accessories. Often it is simply referred to as “white plastic”. Among FDM filaments, the layer bonding of nylon is stronger than all others, making it the ideal 3D printing material for parts that require good tensile and mechanical strength.Some of the Nylon grades in 3D Printing as follows:PA6 or PA66 : Fused Deposition Modelling (FDM) & Selective Laser Sintering (SLS)PA12- Multi Jet Fusion (MJF) by HPPA 11- SLS
PET:
The material water bottles are made of. This material is the second alternative to ABS. Unlike ABS, PET does not emit odorous fumes when melted but it is just as strong and flexible. More importantly, PET does not require a heated bed. This material has a glossy finish and is food safe which makes it a popular choice for many consumer products.This material is used in thermoforming processes. It can also be combined with other materials like glass fiber to create engineering resins.It melts at around 230 degrees C and cools into a rigid solid resembling glass. It can be dyed while maintaining its glass-like characteristics, therefore it is available in a variety of colors. It is strong and resilient but has to be printed slowly to make sure the layers adhere properly.HIPS:HIPS or High Impact Polystyrene are plastic filaments that are used for support structures in FDM printers. It is comparable to ABS when it comes to ease of use. The only difference is its ability to dissolve.HIPS has two applications: It is often used as a support material in FDM and SLA printing because it dissolves in the chemical Limonene.HIPS is also an extremely durable material that is suitable for shipping containers or other applications that require high impact resistance. Note that HIPS emits vapors when printed.
Resins:
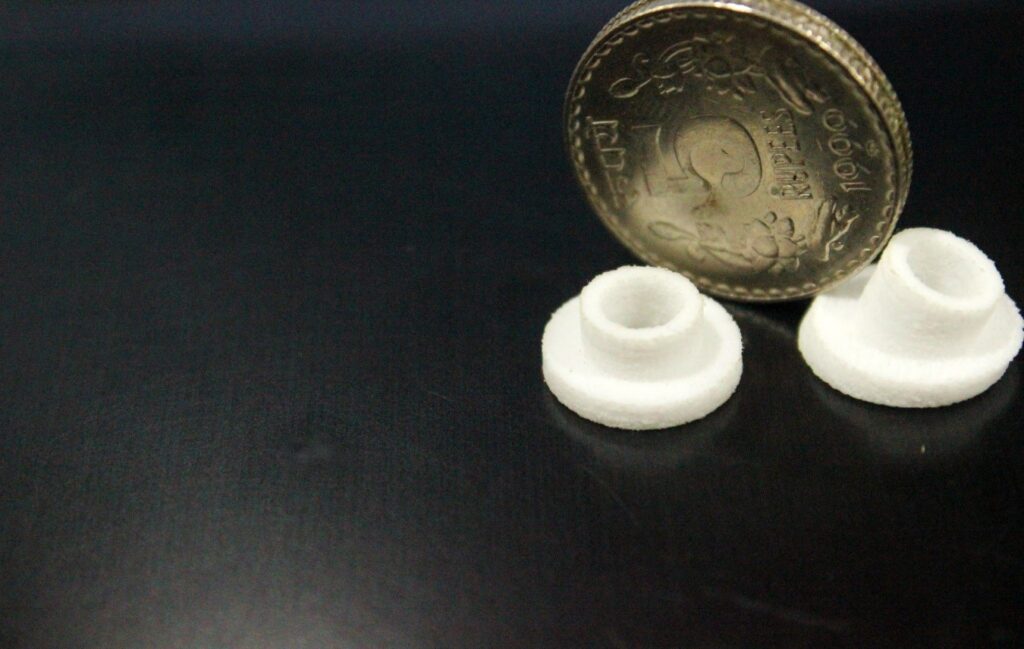
Resin is one of the most used materials in 3D printing. It is mainly used in technologies such as SLA, DLP, Multijet or CLIP technologies. Resin offers limited flexibility and strength. Made of liquid polymer, resin reaches its end state with exposure to UV light. Resin is generally found in black, white and transparent varieties, but certain printed items have also been produced in orange, red, blue and green.Resins work well for functional and concept models; they can be used to produce large parts in a short time with a high degree of detail. High-temperature resins are a cost-effective way of producing injection molds for the small-scale production of prototypes.At Amuse, we recycle all the plastic waste to maintain low carbon print from our facility. Thus, thermoplastics we generate are recycled at ease. However, one problem we face with resin is recycling challenge. Then what we do SLA part wastes? We are working with a couple of plastic incineration companies to convert into fuel.Click here to reach us