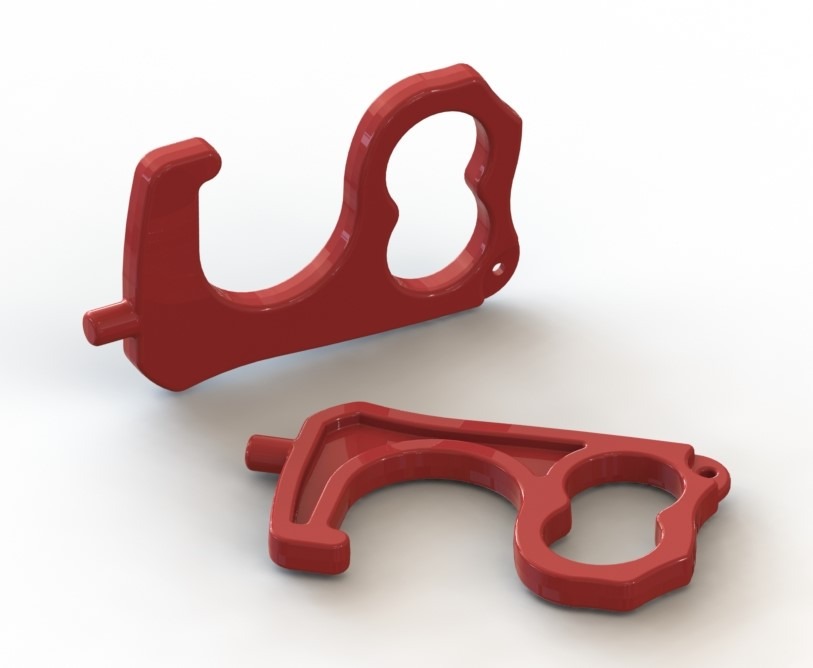
Precision engineering demands a perfect balance between form and function. When it comes to injection moulded parts, achieving a good surface finish is one of the aspects that contribute to the overall success of the end product. The surface finish of an injection moulded part can affect its functionality and aesthetics, as well as its ability to withstand wear and tear. In order to meet the high standards of modern industries, it is essential to optimize the surface finish of injection moulded parts.Here we are! In this article, we will take a deep dive into the various factors that affect the surface finish in injection moulded parts and how to optimize it. We will also find the different techniques, standards, and tools that are used to achieve a desired surface finish. Whether you are a product designer, engineer, or manufacturer, this article will provide you with valuable insights to improve the surface finish of your injection moulded parts.
Factors affecting the surface finish of Injection Moulded Parts
The following are some of the main factors that can affect the surface finish of injection moulded parts:
- Mould design
- Material choice
- Processing parameters
- Post-processing
- Tooling
Mould design: The mould design can have a significant impact on the surface finish of the part. The type of mould, the gating system, the venting system, and the location of the gates and vents can all affect the surface finish.Material choice: The type of material used for injection moulding can also impact the surface finish. Some materials may require different processing parameters to achieve a certain surface finish, while others may have inherent limitations in their ability to achieve a certain level of finish.Processing parameters: The processing parameters such as the temperature, pressure, and injection speed can also impact the surface finish of the moulded part. For example, higher injection speeds may result in a rougher surface finish.Post-processing: The post-processing techniques used on the part, such as polishing or texturing, can also affect the final surface finish.Tooling: The type and quality of tooling used for injection moulding can also impact the surface finish of the part. Higher-quality tooling can often result in a smoother surface finish.By taking into account these factors and optimizing the injection moulding process accordingly, it is possible to achieve a high-quality surface finish in the final product.
How to overcome the factors affecting the surface finish?
Here are a few things that we can do in order to overcome the flaws.
- Mould design optimization: Ensuring proper mould design and construction can help reduce the occurrence of defects that can negatively impact surface finish.
- Change in material selection: Choosing the right materials for the application can improve surface finish by reducing the occurrence of warping, sinking, and other defects.
- Process optimization: Proper process optimization can help minimize the occurrence of defects and improve surface finish. This involves adjusting injection speed, pressure, and temperature.
- Surface finishing techniques: Various surface finishing techniques can be used to further improve surface finish, including sanding, polishing, and coating.
- Mould maintenance: Proper mould maintenance, including regular cleaning and lubrication, can help improve surface finish and reduce the occurrence of defects.
The steps involved in optimizing and improving surface finish include:
- Identifying the factors that are negatively impacting surface finish.
- Developing a plan to address these factors, which may involve mould design changes, material selection, or process optimization.⦁
- Implementing the plan, which may involve making adjustments to the injection moulding process or using surface finishing techniques.
- Regularly monitoring and maintaining the mould to ensure a consistent and high-quality surface finish.
Standards of surface finish
The Society of Plastic Industry (SPI) has created standards for surface finishes of injection moulded plastic parts. These standards provide a way to communicate the desired surface finish between the designer, mould maker, and moulder. The SPI standards use a set of symbols to specify the surface finish, texture, and other details. The symbols consist of a letter and a number, with the letter indicating the surface roughness and the number indicating the maximum allowable texture depth.The SPI mould finish standards range from A-1 (the highest) to D-3 (the lowest). By specifying an SPI standard, all parties involved in the process can work towards achieving a consistent and repeatable surface finish on the final product. This standardization is important in ensuring that the desired surface finish is achieved consistently and efficiently across different parts and manufacturers.
The surface finish is graded as follows:
SPI GradesSurface Finish TypeRoughnessMaterialsAGlossy< 0.05 μmABS, PC, PC/ABS, PPBSemi Glossy0.05 μm - 0.1 μmABS, PC, PC/ABS, PPCMatte0.1 μm - 0.2 μmPA6, PA66, PBT, PC, PC/ABS, Nylon, PP, PS, PVCDTextured0.2 μm - 0.3 μmABS, PP, TPU, Nylon
Conclusion
In conclusion, optimizing the surface finish of injection moulded parts involves various steps that help in achieving high-quality functional products. By understanding and controlling these factors, manufacturers can improve the surface finish of injection moulded parts to meet specific requirements and standards. With the standardization of surface finish by the Society of Plastics Industry (SPI), manufacturers can easily communicate and achieve consistent results. For industry-level 3D printed parts with excellent surface finish, check out Amuse.