HP MJF 3D Printing Service
Precise, Strong & High Quality End Use Parts (from 1 to 10000 units) in 2 to 3 days.
.avif)
.avif)
HP Multi Jet Fusion
Multi Jet Fusion (MJF) is an advanced 3D printing process created by HP. It uses several jets to selectively apply fusing and detailing chemicals to a powdered material, resulting in high-resolution, long-lasting components. MJF has remarkable speed, accuracy, and versatility, perfect for quick prototyping and production-level manufacturing. Explore the future of additive manufacturing with HP’s game-changing Multi Jet Fusion technology.
This very efficient process enables the production of functional and intricately designed parts. Each 80-micron-thick layer contributes to the mechanical strength of the final product, which is similar to injection-moulded parts.
This modern production process removes traditional manufacturing limitations and saves you from costly tooling investments. What’s more? You can receive your parts within days, make design changes as necessary, and deliver your products to market faster. This flexibility and quick turnaround time give you a competitive advantage and the ability to adapt swiftly to market demands.
We are proud to be the best MJF 3D Printing services in India with dedicated experts in Bangalore, Hosur, Hyderabad, Pune, Mumbai, Coimbatore and Delhi. Start prototyping with MJF, and confidently shift serial production with MJF.
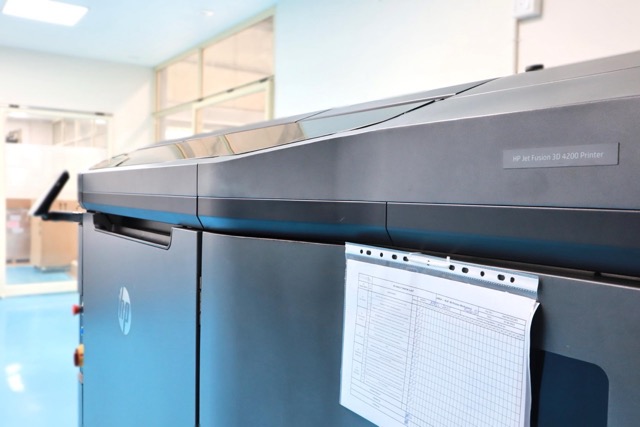
Amuse 3D - Your Serial Production Specialist
Engineering, Quality, and Reliability – that’s what differentiates us. With our automotive production experience, we have attained IATF 16949 qualification, the highest level of quality in working with advanced standards and traceability. We maintain this standard consistently with our MJF 3D Printing, as it reflects our commitment to whatever we do. We are proud to be HP-certified partners worldwide as Multi Jet Fusion Production Professionals for printing advanced quality parts.
Shipping globally from India with quality, love, and care!
One of the largest MJF 3D Printing Machine Fleet
Our expert team is extremely committed to delivering high-speed production and cost-effectiveness. From prototyping to production, we want our customers to have the best offer in any part of their value stream That’s why we have made a strategic decision to invest in the cutting-edge HP MJF 5200 (X2) and 4200, the most advanced polymer system available in the market. With this state-of-the-art HP MJF 3D printing process, we ensure superior results and unmatched efficiency for your manufacturing needs.
Available Materials: PA12, PA11, and PA12GB
Build Size : 380mm * 284mm * 380mm
Dimensional Accuracy: ± 0.3% with a lower limit of ± 0.3 mm
Post Processing Options: Industrial Painting, blasting, UV & pad Printing, and Smoking
Standard Lead time ( at your door) : 3 to 5 days within India, 4 to 7 days Worldwide. We extensively ship MJF parts to the USA, Switzerland, Japan and many other countries in the EU.
.avif)
Consider MJF when you
Make end-use parts from 1 to 10000, alternative to Injection moulding
Manufacture parts in batches for your pilot run
Need parts in quick turnaround time resulting faster goto market.
Want flexible manufacturing
.avif)
Surface finishes for MJF 3D Printing
We offer a range of surface finishing options, sometimes to mimic moulded finish. These finishes enhance both the aesthetic and functional qualities of printed parts. Besides, we have other advanced post-processing techniques
.jpg)
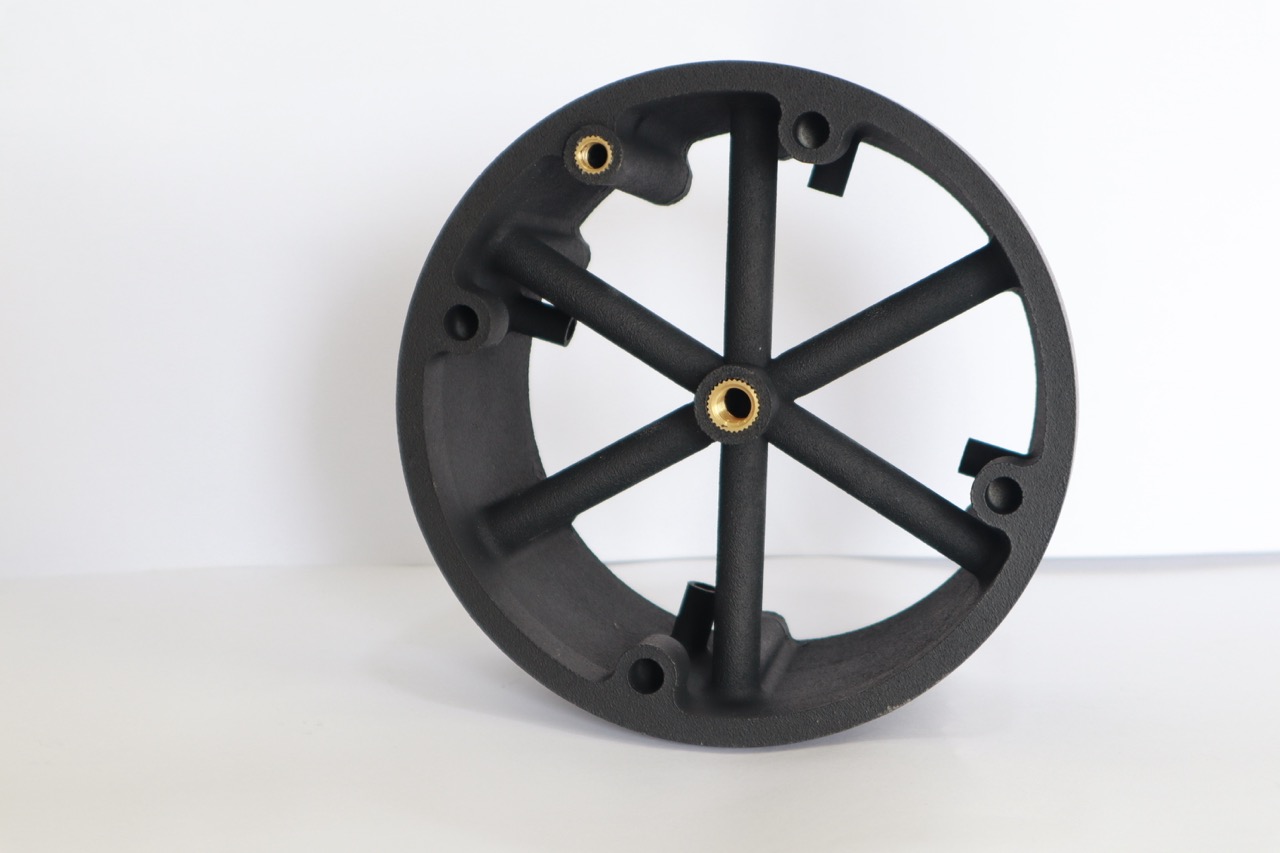
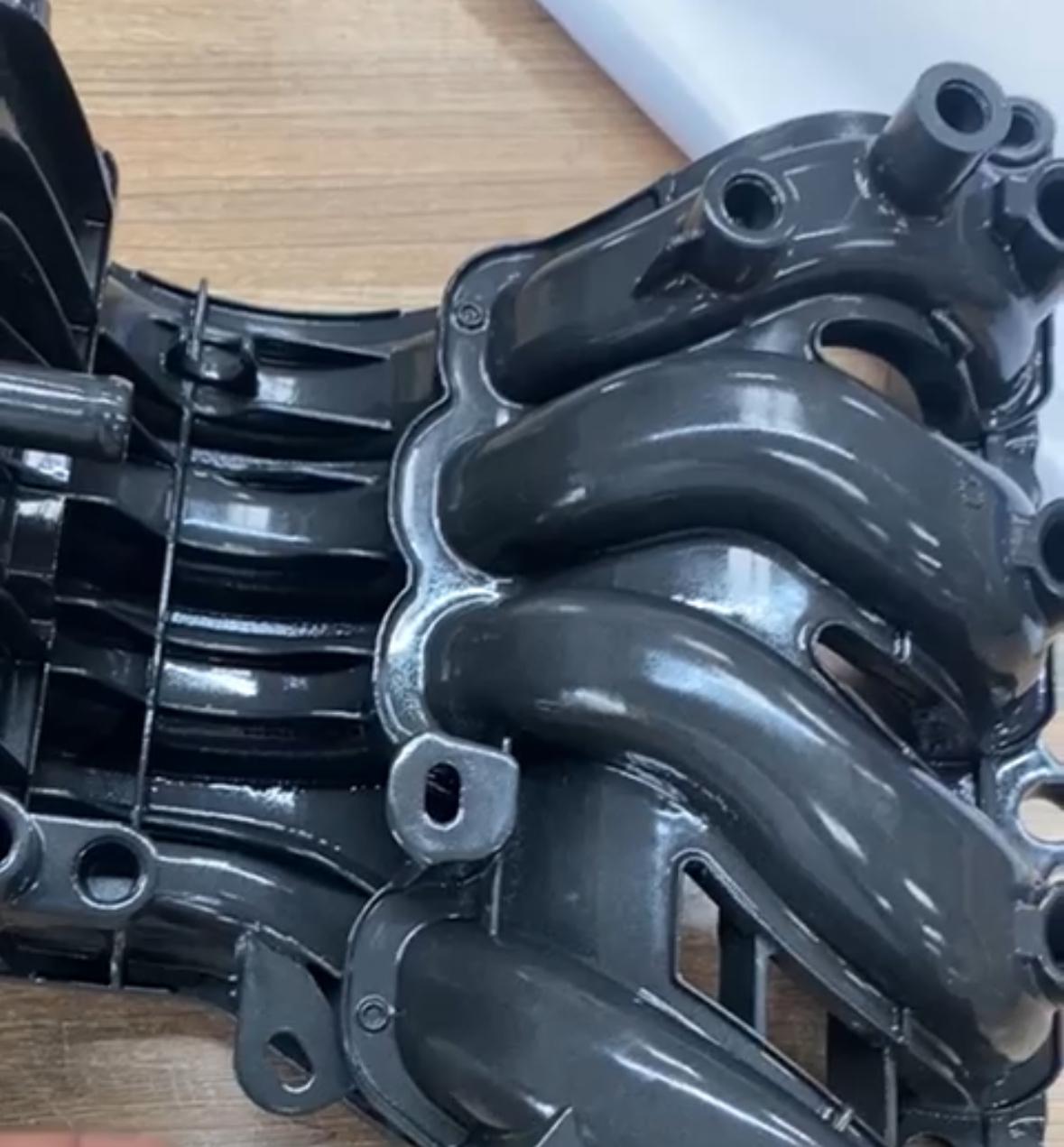
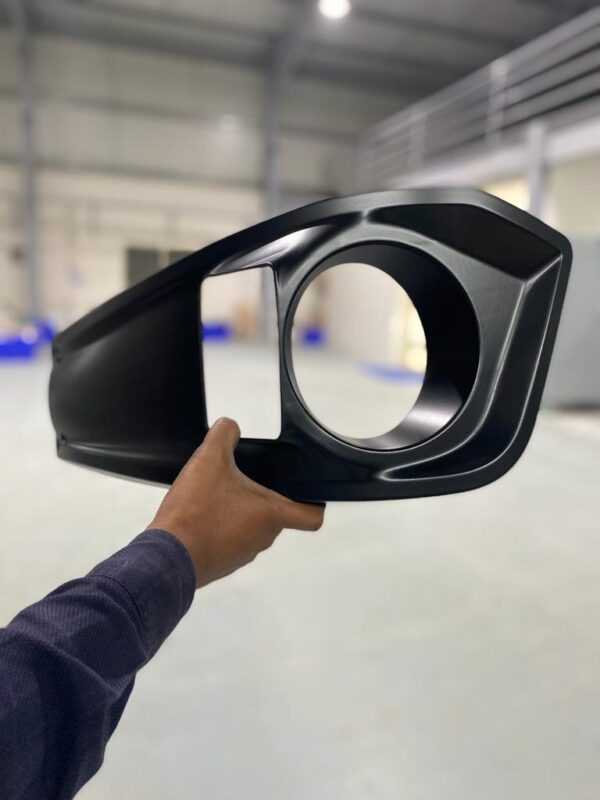
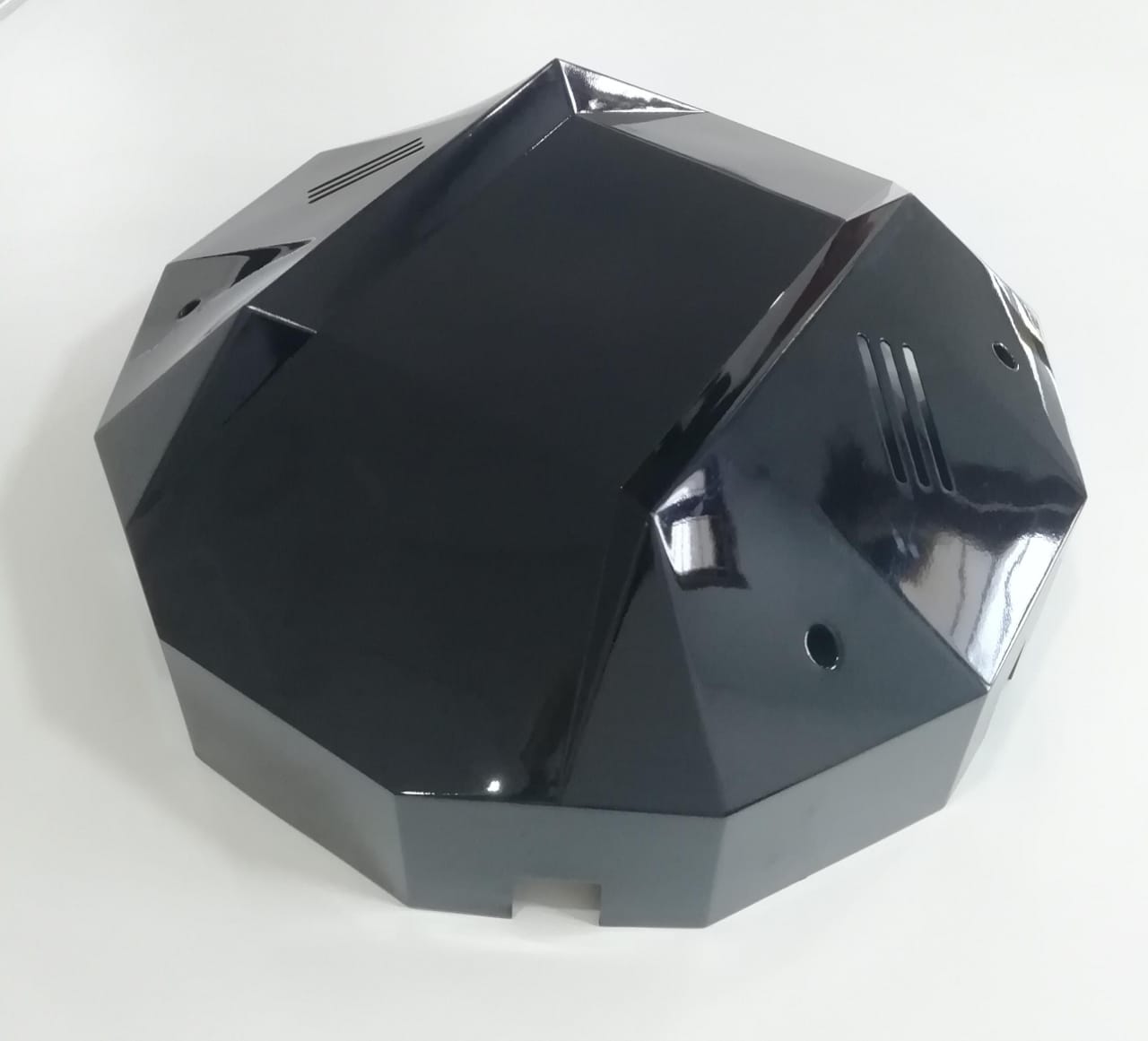
.avif)
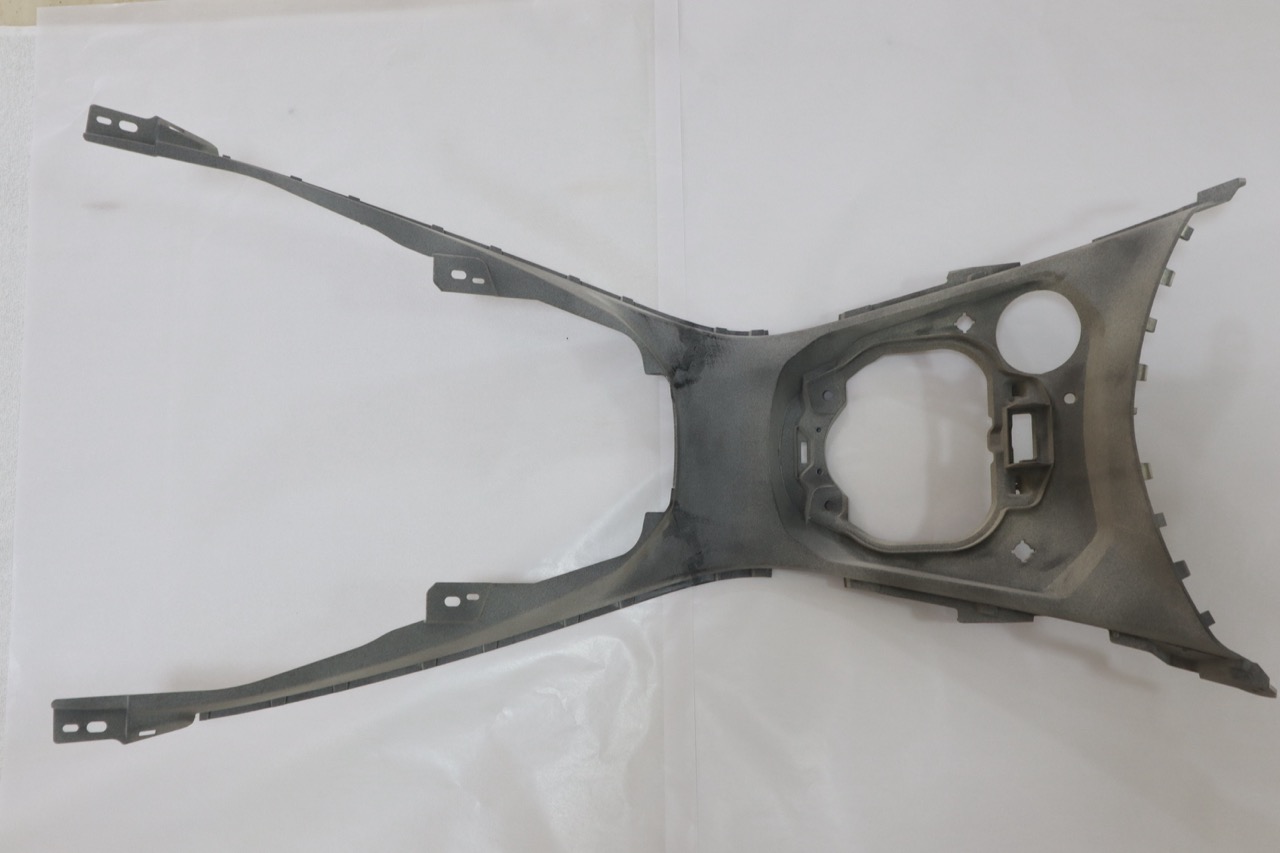
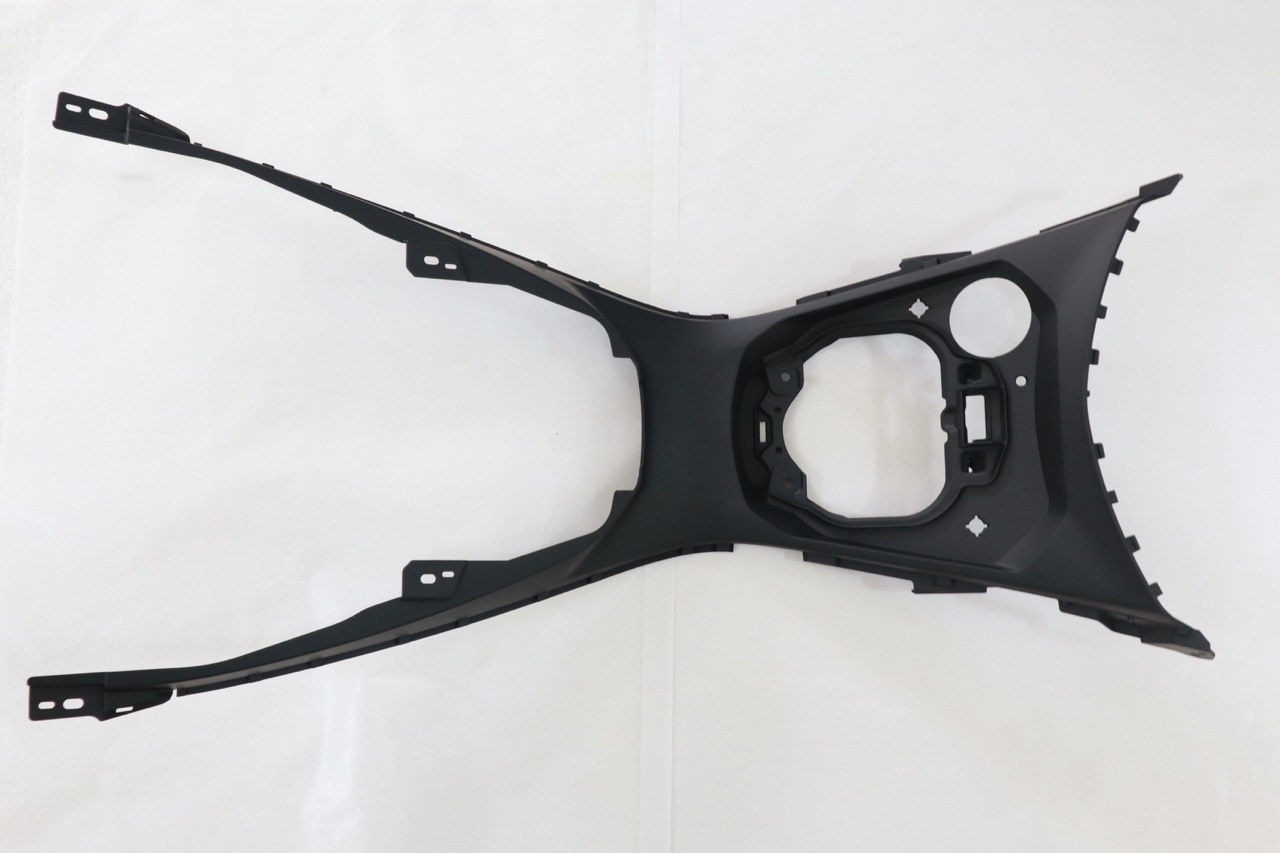
MJF Express
.png)
Your high-quality MJF 3D printed parts dispatched in 24 hrs.
Choose our express option for faster delivery of urgent prototypes or low-volume parts. How? We reserve emergency short builds for last-minute jobs. Order by 2:30 Pm (IST), and we’ll ship your parts within 24 hours. Available material: PA12.
.jpg)
Unlock your free 3D printed samples today
We believe in delivering excellence from the very start. That’s why we offer HP MJF 3D printed samples of your part to validate. Try before you buy, and experience the difference in precision and quality with MJF 3D Printing. Upload your model or request our part.
.avif)
General inquiries? Questions about engineering? Do you seek support with your design?
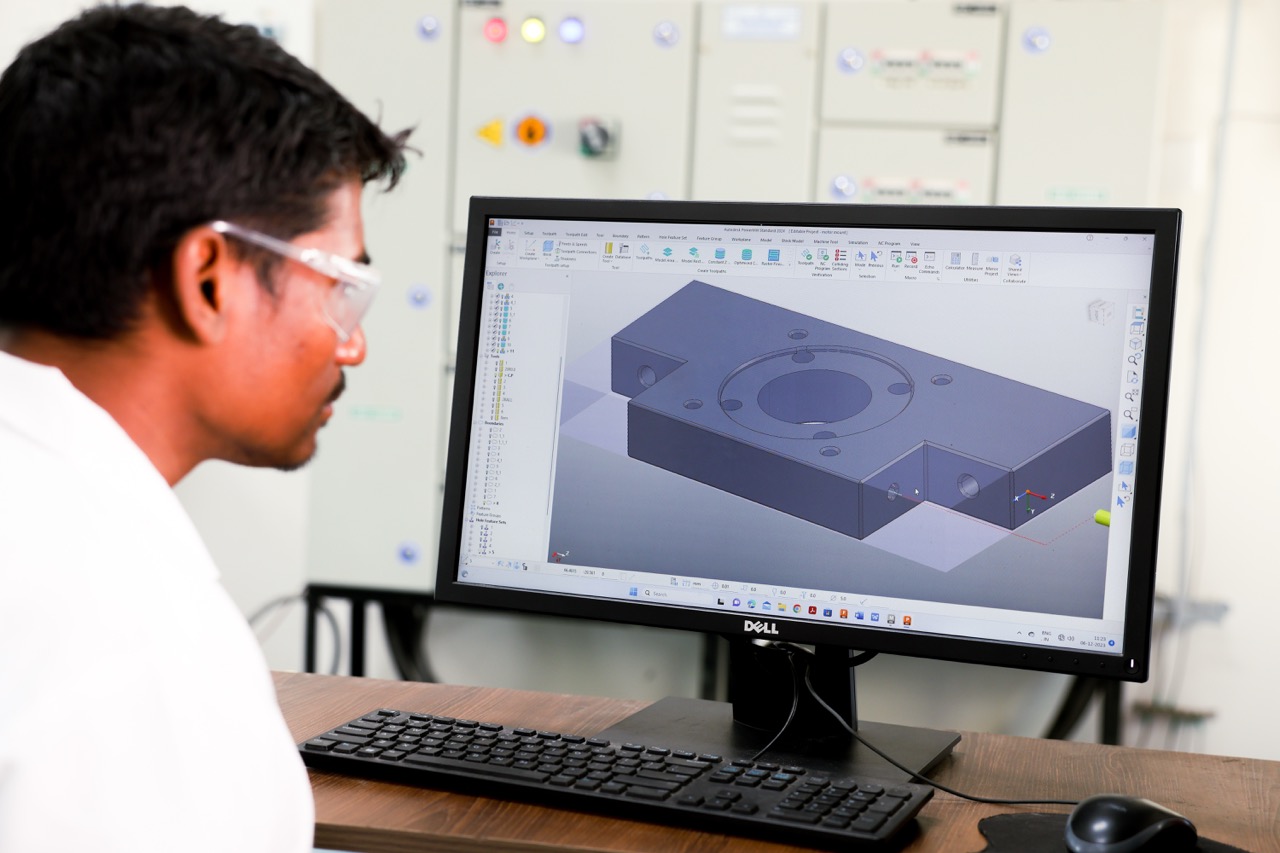
.png)
How MJF is compared to other 3D Printing technologies?
Frequently Asked Questions
Can I confirm my order with PO or email confirmation without upfront payment?
Yes, that works.
You can confirm your order by sending us a purchase order or email confirmation. No upfront payment is required—we’ll proceed accordingly.
However, you will have to either execute a few orders with us or have a credit approval from our team.
The maximum credit days you can avail would be net 30 from the invoice date. For CNC or tooling projects, it's a straight 50% advance, 30% upon T0, and the remaining before dispatch.
Can I share my feedback of the order?
At Amuse 3D, listening to customers isn't just a principle; it's how we do things. The way Amuse 3D interacts with customers—by listening, adapting, and changing—has had a big effect on how we deliver our services.
Each order is a chance to grow and learn, not just a delivery. We can improve our process with your advice, worries, or even minor observations. Your opinions on this order are greatly appreciated, as they help us create a better experience for you and all of our customers.
Whether it's about the print quality, packaging, delivery, or something else entirely. Feel free to express your opinions. That is how we continue to raise the standard.
We send feedback links pertaining to each to hear how you feel. Also, you can send us the feedback via email info@amuse3d.in
If you feel you have a problem with the lot, feel free to raise a complaint ticket with our customer success team; we will resolve it in 24 to 48 hours.
How do I track my package?
As soon as your order ships, Amuse customer support will send you a separate email with your tracking number and dispatch details and full part photos associated with your sales order.
You can also find your tracking number by clicking on your order number in your account and scrolling all the way down.
How to keep embossed adn engraved features for MJF part?
Embossed & Engraved Features
With HP Multi Jet Fusion technology, people can print letters and drawings with very high resolutions and definitions that look like they were embossed or engraved. Any text, number, or drawing in a part should be at least 1 mm deep or high for the best possible output.
- Min height/depth: ≥ 1 mm
- Min font size: 6 pt
- Min feature width: 0.1 mm
How to design solid part for MJF?
With HP Multi Jet Fusion technology, you can print designs that are optimized for topology or even small lattice structures. This design lets you make thinner sections that hold less heat and radiate it back out, which makes the parts more accurate and better looking overall.
Compared to fully solid designs, it also helps to lower the weight of the part, the amount of material, and the fluid agent used. This not only lowers the cost of the part, but it also lowers the cost of running the part in applications where weight is very important.
Parts that are hollow:
This design optimization strategy uses an automatic process to make the model hollow. (Professional software like SolidWorks, Materialise Magics with Materialise Build Processor for HP Multi Jet Fusion technology, and Autodesk® Netfabb® already has this feature.) The walls should be at least 2 mm thick, but thicker walls have better mechanical properties. The best choice depends on how it will be used.
You can add drain holes to the hollow part after the model has been printed to get rid of the powder that is stuck inside. If not, the powder that isn't fused can get stuck in the part, making it heavier and stronger than the fully hollow option. The part is still light, but it is not as strong as the one that is not hollow. The two materials have different densities, which is why they weigh different amounts.
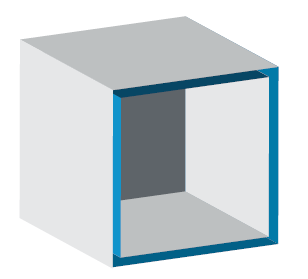
Structures with a lattice:
This design optimization strategy involves hollowing out a part and replacing the solid mass inside with a lattice structure. This structure provides mechanical integrity through the combined action of many rigid cells, while also significantly lowering the part's weight and cost.
This redesign is also quick and can be done automatically with professional software like nTopology or Materialise Magics.
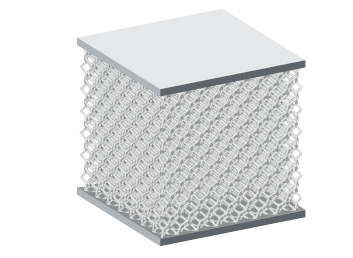
Topology optimization:
Topology optimization is a process based on the finite element method (FEM) that finds the best way to spread out material based on a set of constraints and an optimization goal. Reducing weight and making specific mechanical properties are common goals of optimization. The designer needs to know a lot about how the part works and how the load is spread out, but this is the best way to lower the weight and cost of the original design.
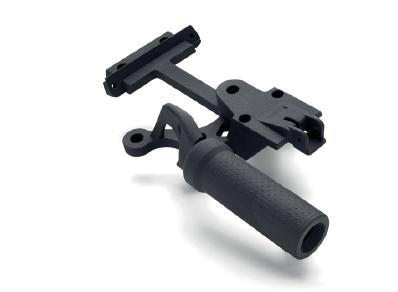
Summary:
.avif)