
Over the years, plastic designers and engineers have been moving towards simple yet powerful design options. One of a kind is the living hinge feature. In this document, we want to highlight key insights and design considerations so that you can flawlessly implement a living hinge. And dramatically improve efficiency.
In our daily life, we see living hinges predominantly in consumer products such as bottle caps, compact makeup containers, peppermint boxes, and electronic cases, to name a few. But why do we need them? To justify this, we have the following reasons.
- Low cost to manufacture
- Minimal wear and tear
- Longer lifespan – durable and stable
- Reduces your assembly time and effort
- Convenient to use
Living Hinge for Injection Moulding
Over time, engineers have optimized the design of living hinge significantly. A basic design is emphasized on key factors below.
[caption id="attachment_31219" align="aligncenter" width="264"]
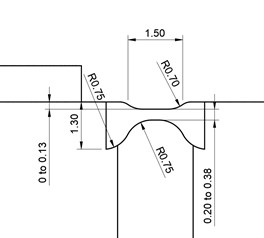
Figure 1 The basic geometry of an injection-moulded living hinge (All dimensions are in mm)[/caption]
Basic Design Geometry for Living Hinge
Three critical design details ensure the success of living hinge:
- The thickness of the hinge (A): The thickness of the hinge is the most critical parameter. It determines the force required to operate and hence the feel of the hinge. If the thickness is too small, the hinge feels too soft. On the other hand, a thicker hinge will be very stiff and shorten the life span.
- Radius on the outer side of the hinge(B): When the hinge is closed, it creates tension on the outer side and compression on the inner side of the hinge. Therefore, a long-curved shape on the outer side reduces the stress concentration during the opening and closing of the hinge.
- Depth of the flat recess (C): The flat recess on the top portion allows the two components to fit together by creating a small opening for the deformed hinge. Besides, it avoids the sharp bending of the hinge.
Materials for living hinge for injection moulding
The most used material for the living hinge is Polypropylene. A good living hinge made of PP can withstand millions of cycles without deforming permanently. Apart from PP, Polyethylene is widely used as it has similar properties to Polypropylene.
Mould for living hinge for injection moulding
- Since the thickness of the hinge determines the force required to operate the hinge. In most cases, the thickness is altered after the first sample to achieve the right feel. Hence it is always advised to take a safe steel approach, i.e., minimum thickness and maximum recess depth. So that later the depth of the recess can be reduced to increase the thickness of the hinge.
- The location and type of gate also play a significant role in moulding a successful living hinge. The gate must be positioned so that the molten plastic flows across the hinge perpendicular to its length.
- The essential rule in injection moulding is to maintain uniform thickness. But in living hinges, by default, we have a thin layer of plastic connecting the two parts. This process may lead to incomplete filling of the cavities due to the differential pressure created between them. One of the methods to avoid this is to provide a separate gate on both cavities.
- Weld lines at the hinge region have to be avoided. So, when providing multiple gates, attention has to be paid to avoid weld lines at the hinges.
Guidelines for Prototyping with 3D Printing
Living hinge for prototyping purposes can be manufactured by 3d printing technologies such as Fused Deposition Modelling (FDM), Material Jet Fusion (MJF) and Selective Laser Sintering (SLS). Generally, 3D printed parts are anisotropic (i.e.) parts are built layer by layer; hence the strength and the cycles that the hinges can withstand is relatively low compared to their injection-moulded counterparts. However, 3D printed living hinges are easier to design and can be altered and iterated numerous times to optimal functionality based on the tolerances of the 3D printer you intend to use.
[caption id="attachment_31220" align="aligncenter" width="434"]
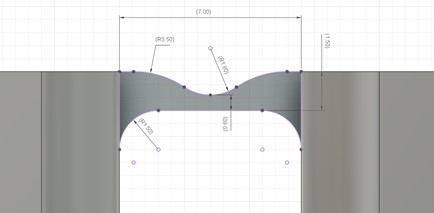
Figure 2 Dimensions of an FDM 3D printed living hinge[/caption]
Hinge Geometry
Generally, a thin strip of material connecting both the hinged parts will be enough for a living hinge. Still, if the hinge is needed to open and close several times without breaking, the following geometry can be implemented.
Part Geometry
Since the parts are Anisotropic - recommended to orient where the length of hinge is parallel to the z-axis of the build platform. By doing so, cross-section (width of the hinge) gets built layer by layer, as shown in Figure 3.
[caption id="attachment_31221" align="aligncenter" width="282"]
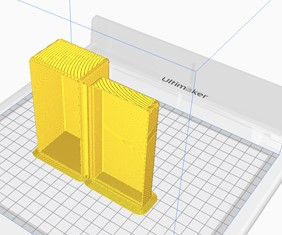
Figure 3 Correct orientation of the part[/caption][caption id="attachment_31222" align="aligncenter" width="263"]
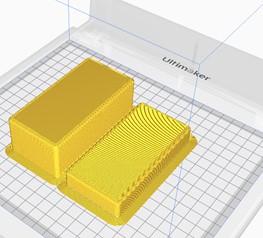
Figure 4 Incorrect orientation of the part[/caption]
Material Selection
The recommended material for printing parts with living hinges are listed below.
Technology
Material
FDM
Nylon or TPU
SLS
Nylon 12 or 11
MJF
Nylon 12
Closing Thoughts
We hope for our commitment to striving to be the most eco-centric company globally and aiding our partners to be the most sustainable company in product development to market launch.
We hope this white paper/blog has given you some ideas about designing a proper living hinge with high confidence. Above all, we are always here to help you with your product design and development in all stages. Please don’t hesitate to contact us.
Source: Fictiv, Plastics today, MIT Living hinge design, Machine Design, Hubs manufacturing
To start your first project with Amuse, Click here
Let's Get Started
Upload your part for 3D Printing https://www.youtube.com/watch?v=J0pE3cGnCX8