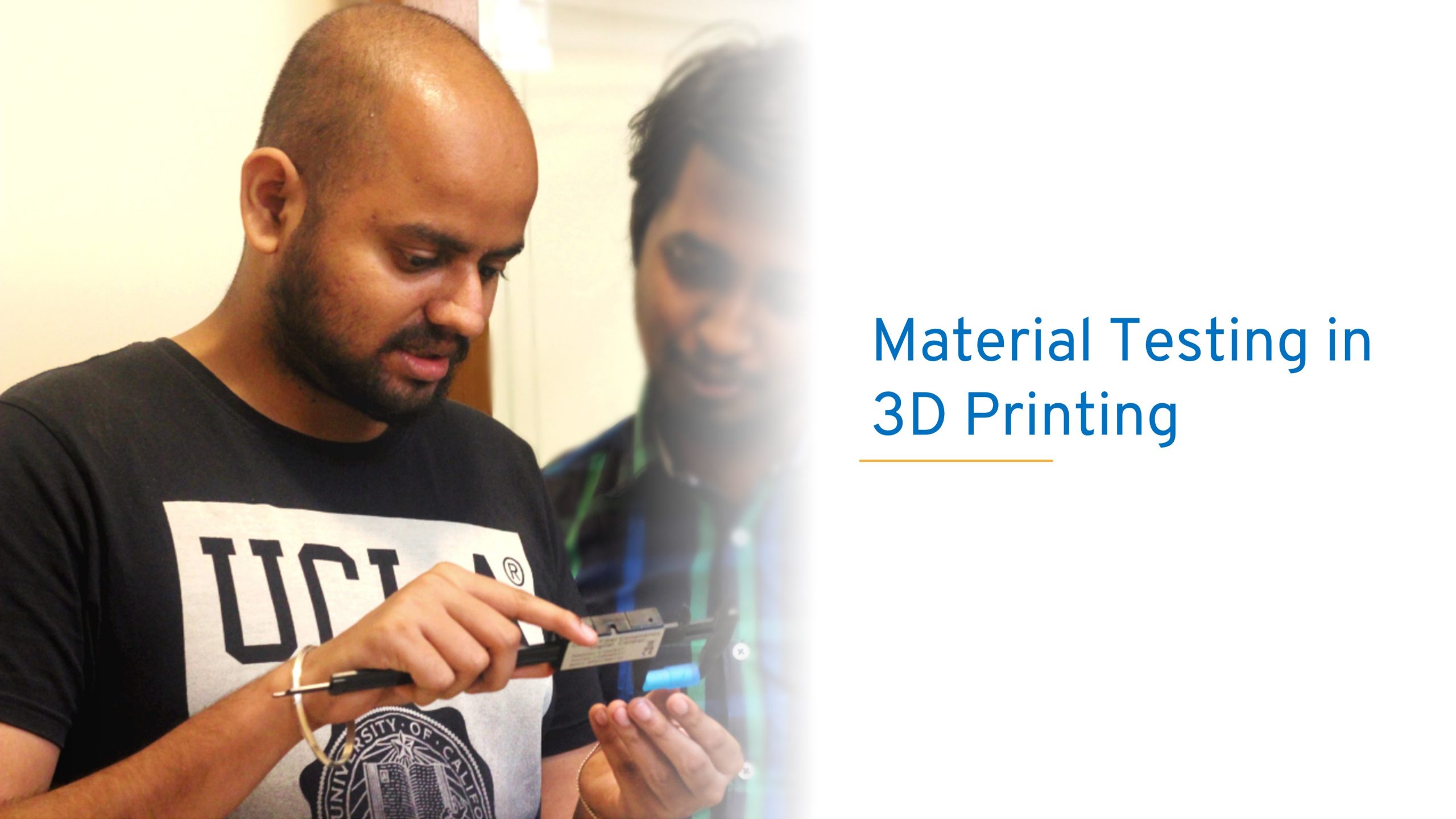
The success of 3D Printing depends heavily on the materials used in the process. Material testing in the 3D printing process ensures that the end product meets the required specifications. Material testing plays a vital role in achieving this objective, as it helps to identify potential flaws in the material and determine its suitability for use in 3D Printing.Material testing in 3D Printing involves various methods and instruments to measure the materials' quality, properties, and performance. It gives insights to identify the strengths and weaknesses of the materials and ensure that they meet the desired specifications for the final product. In this article, we will learn the different forms of material testing used in 3D Printing, their significance, and how they contribute to ensuring the durability of the final printed product.
What is Material Testing?
Material testing is the process of evaluating the physical properties of materials to determine their suitability for a specific application. In 3D Printing, material testing involves evaluating the physical properties of the materials used in the process, such as strength, elasticity, and durability, to ensure that the final part adheres to the required specifications.
Importance of material testing in 3d Printing
Material testing in the 3D printing process helps ensure the durability of the 3D printed parts and how they survive in rough conditions. It also helps to identify any weaknesses or defects in the material which could compromise the final product's performance. Material testing also ensures that the material's properties are consistent, and any variations are identified and addressed as soon as the testing process ends.
Types of Material Testing in 3D Printing
There are several types of material testing done in 3D Printing, including:
Tensile Testing
Tensile testing is a type of material testing that involves applying force to a material until it breaks. This test is used to determine the strength and elasticity of the material.
Compression Testing
Compression testing involves applying a force to a material from two opposite directions to determine its compressive strength. This test is crucial for materials subjected to pressure or impact.
Fatigue Testing
Fatigue testing involves subjecting a material to repeated stress and monitoring how it responds over time. This test determines the durability and resistance of a material to wear and tear.
Thermal Testing
Thermal testing involves subjecting a material to high or low temperatures to determine its resistance to heat or cold.
3 Point Bend Testing
The 3 Point Bend Flexure Test is a material testing method that evaluates a material's flexural strength and stiffness by subjecting it to a three-point bending load.
Factors Affecting Material Testing in 3D Printing
Several factors can affect material testing in 3D Printing, including:
- Print Settings: The print settings used in 3D Printing can significantly affect the material properties. Layer height, infill density, and print speed can all impact the material's physical properties.
- Post-Processing: Post-processing in 3d printing can also affect material properties. Heat treatment, for example, can alter the material's strength and durability.
- Material Variations: Even with careful control of the printing process, there can be variations in the material properties due to differences in the material batches or suppliers.
Case study
A case of using HP Multi Jet Fusion (MJF) 3D printing technology. It is a powerful tool for producing high-quality, functional parts. The technology uses a powder bed fusion process to build up layers of material, resulting in parts with excellent mechanical properties, such as high strength and durability. However, the properties of 3D-printed parts can vary significantly depending on the materials used and the printing parameters applied. Material testing is essential to ensure that 3D-printed parts meet the required standards for specific applications. This case study explores the material testing process with HP MJF 3D printing technology.
The Challenge:
A company that produces custom components for the aerospace industry was looking to use HP MJF 3D printing technology to create lightweight, high-strength parts for use in aircraft engines. Previously, the company relied on traditional manufacturing methods, such as CNC machining and injection molding. However, they wanted to explore the potential of 3D printing to produce parts with complex geometries that would be difficult or impossible to manufacture using traditional methods. The challenge was ensuring that the 3D-printed parts would meet the strict material requirements and standards for aerospace applications.
The Solution:
The company undertook a comprehensive material testing program to ensure that the 3D-printed parts would meet the required standards. The program tested various materials and printing parameters using HP MJF 3D printing technology. The company worked with a material testing lab to conduct the tests, which included:
- Tensile testing: The tensile strength of the 3D-printed parts was measured using an Instron tensile testing machine. The test involved applying a gradually increasing load to the part until it failed. The results were compared to the tensile strength of the same material produced using traditional manufacturing methods.
- Fatigue testing: The fatigue strength of the 3D-printed parts was tested by subjecting them to repeated loading and unloading cycles. The test involved applying a cyclic load to the part and measuring the number of cycles it could withstand before failure. The results were compared to the fatigue strength of the same material produced using traditional manufacturing methods.
- Microstructure analysis: The microstructure of the 3D-printed parts was analyzed using scanning electron microscopy (SEM). The analysis provided information on the quality and consistency of the part's microstructure, which can affect its mechanical properties.
- Chemical analysis: The chemical composition of the 3D-printed parts was analyzed using energy-dispersive X-ray spectroscopy (EDS). The analysis provided information on the purity and composition of the material, which can affect its mechanical properties.
The Results:
The material testing program revealed that the 3D-printed parts produced using HP MJF technology met the required standards for use in aerospace applications. The tensile and fatigue strength of the 3D-printed parts were comparable to those produced using traditional manufacturing methods. The microstructure analysis showed that the parts had a consistent and high-quality microstructure, contributing to their mechanical properties. The chemical analysis showed that the material used in the 3D-printed parts was pure and had the required composition for aerospace applications.
Conclusion
In conclusion, material testing is a necessary step in the 3D printing process that cannot be overlooked. By understanding the testing methods and factors that can affect the results, 3D printing professionals can confidently produce high-quality parts. We hope this article has clearly understood how material testing is done in 3D Printing. For top-quality 3D prints, check out Amuse, your one-stop solution for all things 3D Printing.