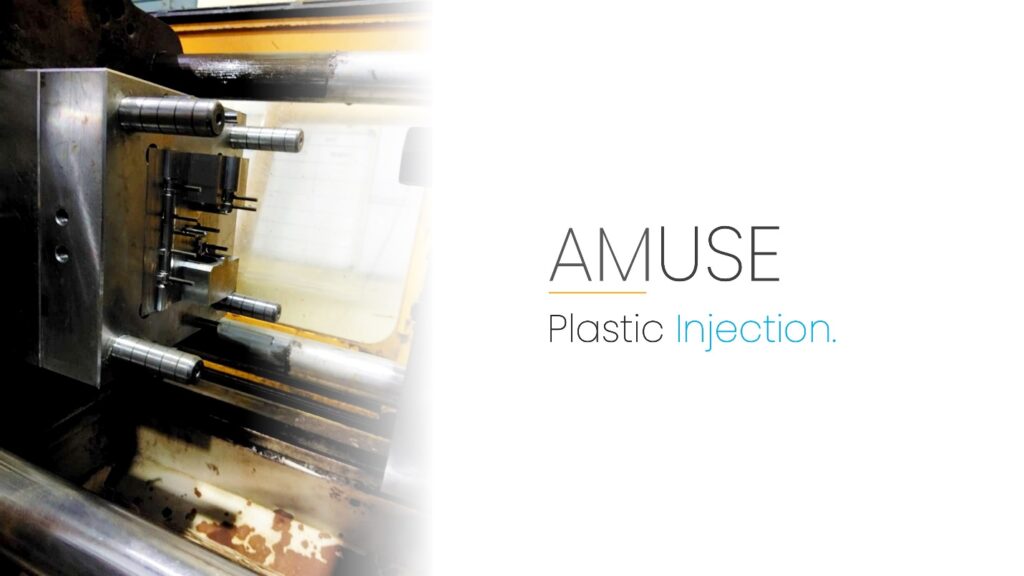
In this section, we will briefly discuss the principle working of injection moulding and its terminologies. With the changing needs and demands of the consumer, manufacturing the goods has also changed. While some products are still manufactured by hand, some use high-end tools and cutting-edge technologies.Injection moulding is the most efficient, economical and scalable technique to manufacture custom plastic parts consistently. The volume of the parts that can be manufactured ranges from hundreds to millions. It also has an extensive portfolio of materials and surface finish options to choose from compared to other methods like CNC machining.Mass production or large scale manufacturing predominantly requires specialized technology and innovation for efficient production and quality while saving time with undiminished precision. One such modus operandi for manufacturing is "Injection Molding".The injection moulding process has four essential steps carried out in cycles to produce plastic parts on a large scale.
- Closing of Mould or Clamping: The two halves of the mould are held together with force. The force depends on the injection pressure or size of the mould.
- Plastic Injection: The plastic pellets are melted and injected into the mould cavity.
- Cooling: The molten plastic material is solidified with the help of coolant channels in the mould.
- Opening of Mould or Ejection: The mould's two halves are opened, and the plastic part is ejected.The time taken to complete the set of operations once is known as the cycle time.
Injection Moulding Nomenclature:
- Mould: A mould usually has two halves – Core (Non-cosmetic side) and Cavity (Cosmetic side). When held together, the two halves of the mould forms the shape of the plastic part to be manufactured. The mould is generally made from hardened tool-grade steel (P20 or H13) or even aluminium.
- Runner: The molten plastic material is injected into the mould cavity from the sprue through the runner system. There are usually two types of runners: Hot runner and cold runner. The solidified runner is automatically trimmed from the part while ejecting in the case of a hot runner. Whereas in the cold runner, it is dependent on the mould construction.
- Gate: The molten plastic enters the mould cavity from the runner through a small opening called a gate. Different type of gates is used depending on the part geometry – Edge gate, Submarine gate, Sprue gate & Diaphragm gate. The type and size of the gate play a significant role in the plastic material filling the mould cavity.
- Air Vents: An air vent is a small channel usually machined in the cavity side of the mould to release the air trapped inside during injection. This process ensures complete filling of the part, and also trapped air sometimes causes burning of plastic.
- Parting Line: A line is formed around the plane where two mould halves meet.
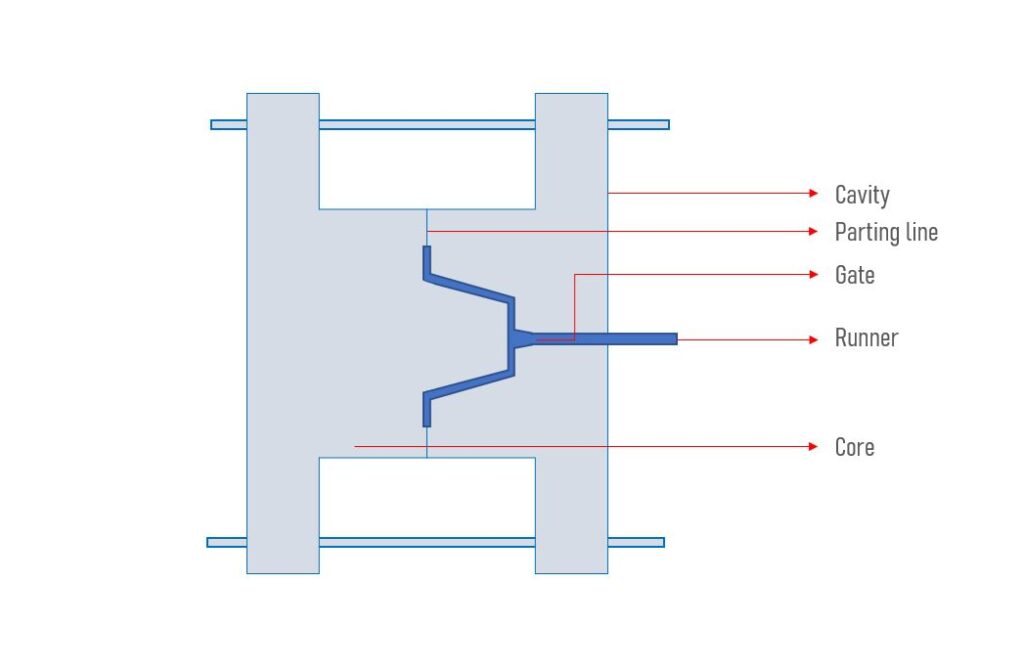
In short, it is a widely practised process of manufacturing for mass production. The process is principally used for thermoplastic materials, which may be successively melted, reshaped and cooled. Injection moulded components are used for almost every useful manufactured article, from automotive products to food packaging. It is a multifaceted process for producing high-quality products varying in complexities on a fully automated basis at high speed. While injection moulding gives the benefit of economies of scale, inefficiency and defects can cause significant losses. Moreover, it is an expensive process with expansive machines and tools making competency and proficiency an unavoidable pre-requisiteClick here to reach us